溶解技術
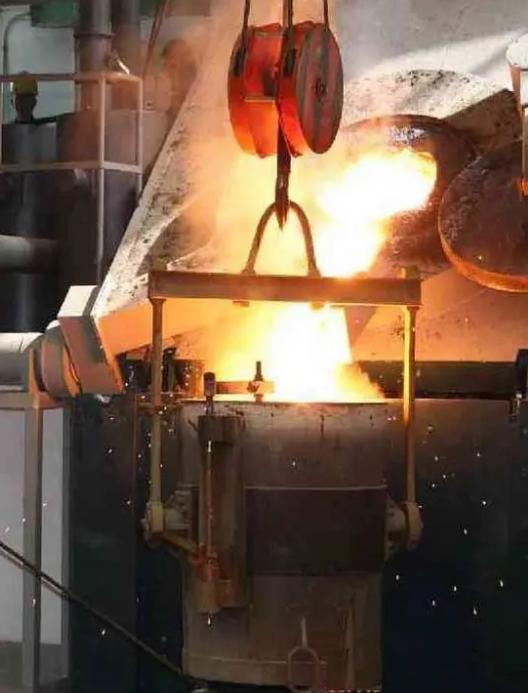
現在、銅加工品の製錬には誘導溶解炉が一般的であり、反射炉製錬やシャフト炉製錬も採用されています。
誘導炉製錬はあらゆる種類の銅および銅合金に適しており、クリーンな製錬と溶湯の品質の確保という特徴があります。炉の構造に応じて、誘導炉はコア付き誘導炉とコアレス誘導炉に分けられます。コア付き誘導炉は、生産効率が高く、熱効率が高いという特徴があり、赤銅や黄銅などの単一品種の銅および銅合金の連続溶解に適しています。コアレス誘導炉は加熱速度が速く、合金種類の交換が容易であるという特徴があります。青銅、白銅など各種銅および高融点銅合金の溶解に適しています。
真空誘導炉は、電気真空用の真空システムを備えた誘導炉で、無酸素銅、ベリリウム青銅、ジルコニウム青銅、マグネシウム青銅など、吸入しやすく酸化しやすい銅および銅合金の製錬に適しています。
反射炉製錬は、溶湯から不純物を精製して除去することができ、主に銅スクラップの製錬に使用されます。シャフト炉は一種の急速連続溶解炉であり、高い熱効率、高い溶解速度、便利な炉の停止という利点があります。制御可能。精製プロセスがないため、原材料の大部分は陰極銅である必要があります。シャフト炉は連続鋳造用の連続鋳造機で使用されるのが一般的ですが、半連続鋳造用の保持炉と併用することもできます。
銅製錬生産技術の発展傾向は主に、原料の燃焼損失の削減、溶湯の酸化と吸入の減少、溶湯の品質の向上、高効率の採用(誘導炉の溶融速度がより速い)に反映されています。 10 t/h以上)、大規模(誘導炉の能力は35 t/セット以上も可能)、長寿命(ライニング寿命は1〜2年)、省エネ(誘導炉のエネルギー消費量は1〜2年)炉は360kW・h/t以下)、保持炉は脱ガス装置(COガス脱ガス)付、誘導炉はセンサーはスプレー構造、電気制御装置は双方向サイリスタ+周波数変換電源を採用、炉の予熱、炉の状態と耐火物温度フィールドの監視および警報システム、保持炉には計量装置が装備されており、温度制御はより正確です。
生産設備 - スリッターライン
銅帯スリッターラインの生産は、幅広のコイルをアンコイラーで広げ、スリッター機で必要な幅にカットし、ワインダーで複数のコイルに巻き戻す連続スリッター生産ラインです。(保管ラック)クレーンを使用してロールを保管ラックに保管します
↓
(積載車) 供給台車を使用して、アンコイラードラムにロール原反を手動で置き、締めます。
↓
(アンコイラーと緩み止め加圧ローラー) オープニングガイドと加圧ローラーでコイルを巻き出します。
↓
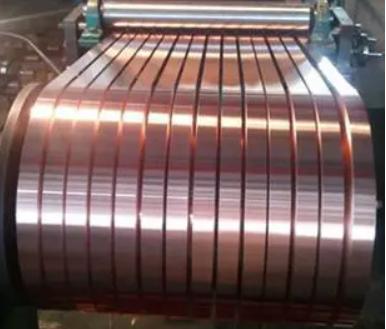
(NO・1ルーパーとスイングブリッジ)ストレージとバッファー
↓
(エッジガイドとピンチローラー装置) 縦ローラーがシートをピンチローラーにガイドしてズレを防ぎ、縦ガイドローラーの幅と位置を調整可能
↓
(スリッター機) スリッター機に入り、位置決めとスリットを行います。
↓
(クイックチェンジロータリーシート) ツール群交換
↓
(スクラップ巻き取り装置) スクラップをカットする
↓(出口エンドガイドテーブルとコイルテールストッパー) NO.2ルーパー導入
↓
(スイングブリッジとNO.2ルーパー)素材の収納と厚み差の解消
↓
(プレスプレート張力と空気拡張シャフト分離装置)張力を提供し、プレートとベルトを分離します
↓
(スリッティングシャー、ステアリング長さ測定器、ガイドテーブル) 測長、コイル定長分割、テープ通しガイド
↓
(巻取機、分離装置、押板装置) セパレーターストリップ、コイリング
↓
(トラック荷降ろし、梱包)銅テープ荷降ろし、梱包
熱間圧延技術
熱間圧延は、主にシート、ストリップ、フォイル製造用のインゴットのビレット圧延に使用されます。
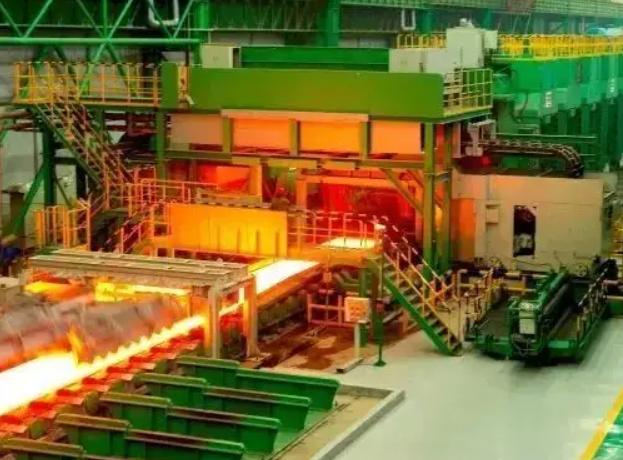
ビレット圧延のインゴット仕様は、品種、生産規模、鋳造方法などの要素を考慮する必要があり、圧延設備の条件(ロール開口部、ロール直径、許容圧延圧力、モーター出力、ローラーテーブル長など)に関連します。 、など。一般に、インゴットの厚さとロールの直径の比率は1:(3.5〜7)です。通常、幅は完成品の幅と同じか数倍であり、幅とトリミング量は適切に調整する必要があります。考慮された。一般に、スラブの幅はロール本体の長さの 80% である必要があります。インゴットの長さは製造条件に応じて合理的に考慮する必要があります。一般に、熱間圧延の最終圧延温度を制御できることを前提とすると、インゴットが長いほど生産効率が高く、歩留りも高くなります。
中小規模の銅加工工場のインゴット仕様は一般的に (60 ~ 150) mm × (220 ~ 450) mm × (2000 ~ 3200) mm、インゴット重量は 1.5 ~ 3 t です。大型銅加工工場のインゴット仕様 一般的には(150~250)mm×(630~1250)mm×(2400~8000)mm、インゴットの重量は4.5~20tです。
熱間圧延では、高温の圧延材にロールが接触した瞬間にロール表面の温度が急激に上昇します。熱膨張と冷間収縮を繰り返すことにより、ロール表面に亀裂や亀裂が生じます。したがって、熱間圧延中に冷却と潤滑を行う必要があります。通常、水または低濃度のエマルションが冷却および潤滑媒体として使用されます。熱間圧延の総加工率は一般に90%~95%である。熱間圧延されたストリップの厚さは、一般に9〜16 mmです。熱間圧延後のストリップの表面フライス加工により、鋳造、加熱、熱間圧延中に発生した表面酸化層、スケール侵入、その他の表面欠陥を除去できます。熱間圧延鋼板の表面欠陥の程度や工程のニーズに応じて、各面のミリング量は0.25~0.5mmとなります。
熱間圧延機は通常、2 段または 4 段の可逆圧延機です。インゴットの大型化とストリップ長の継続的な延長に伴い、熱間圧延機の制御レベルと機能は、自動厚さ制御、油圧ベンディングロール、フロントおよびリアの使用など、継続的に改善および改善される傾向にあります。縦型ロール、冷却せずに冷却ロールのみ 圧延装置装置、TPロール(テーパーピストンロール)クラウン制御、圧延後のオンラインクエンチング(焼き入れ)、オンラインコイリングなどの技術により、ストリップの組織や特性の均一性を向上させ、より良好な特性を得ることができます。皿。
鋳造技術
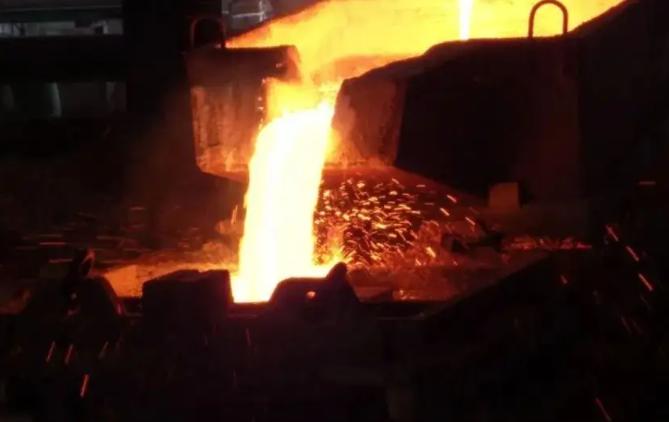
銅および銅合金の鋳造は一般に、垂直半連続鋳造、垂直完全連続鋳造、水平連続鋳造、上向き連続鋳造およびその他の鋳造技術に分類されます。
A. 竪型半連続鋳造
縦型半連続鋳造は、設備が簡単で生産が柔軟であるという特徴があり、銅および銅合金の様々な丸形および平形インゴットの鋳造に適しています。竪型半連続鋳造機の伝達方式は油圧式、リードスクリュー式、ワイヤーロープ式に分けられます。油圧トランスミッションは比較的安定しているため、より多く使用されています。晶析装置は、必要に応じてさまざまな振幅と周波数で振動させることができます。現在、半連続鋳造法は銅および銅合金のインゴットの製造に広く使用されています。
B. 垂直完全連続鋳造
縦型全連続鋳造は、大生産量と高歩留り(約98%)という特徴を持ち、単一品種・仕様の鋳塊を大量に連続生産するのに適しており、溶解・鋳造の主要な選択法の一つとなりつつあります。最新の大規模銅ストリップ生産ラインでのプロセス。縦型全連続鋳造金型は非接触レーザー液面自動制御を採用しています。鋳造機は一般に、油圧クランプ、メカニカルトランスミッション、オンライン油冷ドライチップソーイングとチップ収集、自動マーキング、インゴットの傾斜を採用しています。構造が複雑で自動化度が高い。
C. 横型連続鋳造
横型連続鋳造ではビレットやワイヤービレットを製造できます。
ストリップ横型連続鋳造では、厚さ14~20mmの銅および銅合金ストリップを製造できます。この厚さ範囲のストリップは、熱間圧延を行わずに直接冷間圧延できるため、熱間圧延が難しい合金(錫、リン青銅、鉛黄銅など)の製造によく使用されます。白銅および低合金銅合金条。横型連続鋳造では鋳片の幅に応じて1~4本の鋳片を同時に鋳造できます。一般的に使用される横型連続鋳造機は、幅 450 mm 未満のストリップを 2 つ同時に鋳造することも、ストリップ幅 650 ~ 900 mm のストリップを 1 つ鋳造することもできます。横型連続鋳造ストリップは、一般的にプル・ストップ・リバース・プッシュという鋳造プロセスを採用しており、表面には周期的な結晶化線があり、通常はフライス加工によって除去する必要があります。フライス加工を行わずにストリップビレットを引き抜きおよび鋳造することによって製造できる高表面銅ストリップの国内の例がある。
チューブ、ロッド、ワイヤービレットの水平連続鋳造では、さまざまな合金や仕様に応じて 1 ~ 20 個のインゴットを同時に鋳造できます。一般に、棒材または線材の直径は 6 ~ 400 mm、チューブ素材の外径は 25 ~ 300 mm です。肉厚は5~50mm、インゴットの一辺の長さは20~300mmです。横型連続鋳造法の利点は、工程が短く、製造コストが低く、生産効率が高いことです。同時に、熱間加工性の悪い一部の合金材料にとっては必要な製造方法でもあります。最近では、錫-リン青銅条、亜鉛-ニッケル合金条、リン脱酸銅空調管などの一般的な銅製品のビレットの製造方法として主流となっています。製造方法。
横型連続鋳造法の欠点は、適した合金の種類が比較的単純であること、鋳型内スリーブ内の黒鉛材料の消費量が比較的多いこと、インゴット断面の結晶構造の均一性が低いことである。コントロールが簡単です。インゴットの下部は、金型の内壁に近く、重力の影響により継続的に冷却され、結晶粒がより細かくなります。上部は空隙の形成と高い溶融温度によるもので、インゴットの凝固に遅れが生じ、冷却速度が遅くなり、インゴットの凝固ヒステリシスが生じます。結晶構造は比較的粗く、特に大型のインゴットでは顕著です。上記の欠点を考慮して、ビレットを用いた垂直曲げ鋳造法の開発が現在進められている。ドイツの会社は、垂直曲げ連続鋳造機を使用して、DHP や CuSn6 などの (16 ~ 18) mm × 680 mm の錫青銅ストリップを 600 mm/min の速度で試験鋳造しました。
D. 上向き連続鋳造
上向き連続鋳造は、ここ20~30年で急速に発展した鋳造技術であり、光沢銅線材のワイヤービレットの製造に広く使用されています。真空吸引鋳造の原理を利用し、ストッププル技術を採用することで連続多頭鋳造を実現しました。シンプルな設備、少額の投資、金属の損失が少なく、環境汚染が少ないという特徴があります。上向き連続鋳造は、一般に赤銅および無酸素銅線ビレットの製造に適しています。近年の新たな成果としては、大口径チューブブランク、黄銅、白銅への普及・応用が挙げられます。現在、年間生産量5,000t、直径Φ100mmを超える上向き連続鋳造装置が開発されており、今後も開発が進んでいます。二元普通黄銅と亜鉛白銅の三元合金ワイヤービレットが生産されており、ワイヤービレットの歩留まりは90%以上に達します。
E. その他の鋳造技術
連続鋳造ビレット技術は開発中です。上向き連続鋳造のストッププル工程によりビレット外表面に生じるスラブマーク等の欠点を克服し、表面品位に優れています。また、ほぼ方向性のある凝固特性により、内部構造がより均一かつ純粋になり、製品の性能も向上します。ベルト式連続鋳造銅線ビレットの製造技術は、3トン以上の大型生産ラインで広く採用されています。スラブの断面積は一般に2000 mm2以上であり、その後に生産効率の高い連続圧延機が続きます。
私の国でも電磁鋳造は1970年代から試みられてきましたが、工業生産は実現していませんでした。近年、電磁鋳造技術は大きく進歩しています。現在、Φ200mmの無酸素銅インゴットの表面を滑らかに鋳造することに成功しています。同時に、溶湯に対する電磁場の撹拌効果により、排気とスラグの除去が促進され、酸素含有量が0.001%未満の無酸素銅が得られます。
新しい銅合金鋳造技術の方向性は、凝固理論に基づく方向性凝固、急冷凝固、半凝固形成、電磁撹拌、変成処理、液面自動制御などの技術手段を通じて鋳型の構造を改善することである。、高密度化、精製を行い、連続運転とニアエンド成形を実現します。
長期的には、銅および銅合金の鋳造は半連続鋳造技術と全連続鋳造技術が共存し、連続鋳造技術の適用割合は増加し続けるでしょう。
冷間圧延技術
圧延されたストリップの仕様と圧延プロセスに応じて、冷間圧延は分塊圧延、中間圧延、仕上げ圧延に分類されます。板厚14~16mmの鋳片を冷間圧延し、板厚5~16mm程度の熱間圧延ビレットを2~6mmまで圧延する工程をブルーミングといい、板厚を薄くし続ける工程をいいます。圧延したものを中間圧延といいます。、最終製品の要件を満たすための最終の冷間圧延は仕上げ圧延と呼ばれます。
冷間圧延プロセスでは、さまざまな合金、圧延仕様、完成品の性能要件に応じて圧下システム(総加工率、パス加工率、完成品加工率)を制御し、ロール形状を合理的に選択および調整し、潤滑を合理的に選択する必要があります。方法と潤滑剤。張力の測定と調整。
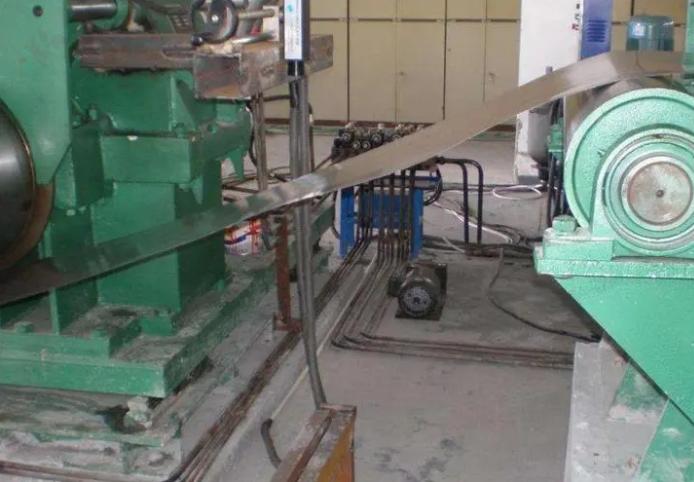
冷間圧延機は通常、4 段または複数段の可逆圧延機を使用します。現代の冷間圧延機は一般に、油圧によるポジティブおよびネガティブロール曲げ、厚さ、圧力、張力の自動制御、ロールの軸方向移動、ロールの部分冷却、プレート形状の自動制御、圧延片の自動位置合わせなどの一連の技術を使用しています。 、ストリップの精度を向上させることができます。最大0.25±0.005mm、プレート形状の5I以内。
冷間圧延技術の発展傾向は、高精度マルチロールミル、より高速な圧延速度、より正確な板厚と形状制御、および冷却、潤滑、コイリング、センタリング、ラピッドロールなどの補助技術の開発と応用に反映されています。変化。精製など。
生産設備-ベル炉
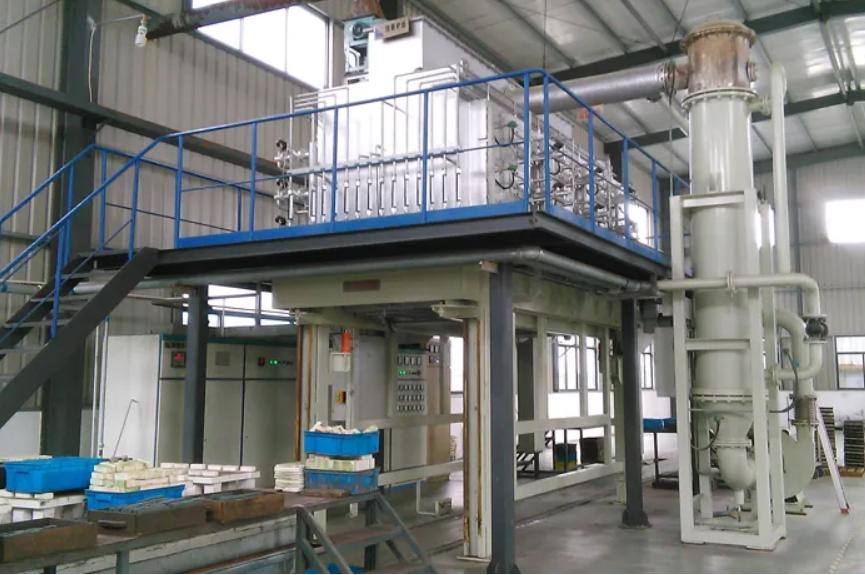
ベルジャー炉と昇降炉は、一般に工業生産やパイロットテストに使用されます。一般に電力が大きく消費電力も大きい。産業企業にとって、洛陽シグマ昇降炉の炉材料はセラミックファイバーであり、優れた省エネ効果、低エネルギー消費、低エネルギー消費を備えています。電力と時間を節約し、生産量の増加に役立ちます。
25年前、ドイツのBRANDS社とフェライト製造業界の大手フィリップス社は、新しい焼結機を共同開発しました。この装置の開発は、フェライト業界の特別なニーズに応えます。このプロセス中、BRANDS Bell Furnace は継続的に更新されます。
彼は、フィリップス、シーメンス、TDK、FDK などの世界的に有名な企業のニーズに注目しており、これらの企業もまた、BRANDS の高品質機器から大きな恩恵を受けています。
ベルファーネスで製造される製品の安定性の高さにより、ベルファーネスは専門的なフェライト製造業界のトップ企業となっています。25 年前、BRANDS によって作られた最初の窯は、今でもフィリップス向けの高品質な製品を生産しています。
ベルファーネスが提供する焼結炉の最大の特徴は、その高効率です。そのインテリジェントな制御システムとその他の機器は完全な機能ユニットを形成しており、フェライト業界のほぼ最先端の要件を完全に満たすことができます。
ベルジャー炉の顧客は、高品質の製品を生産するために必要な温度/雰囲気プロファイルをプログラムして保存できます。さらに、お客様は実際のニーズに合わせて他の製品も生産できるため、リードタイムが短縮され、コストが削減されます。焼結装置は、市場のニーズに継続的に適応するために、さまざまな製品を製造するために優れた調整機能を備えていなければなりません。これは、個々の顧客のニーズに応じて対応する製品を生産する必要があることを意味します。
優れたフェライト メーカーは、顧客の特別なニーズを満たすために 1,000 種類を超える異なる磁石を生産できます。これらには、焼結プロセスを高精度で繰り返す能力が必要です。ベルジャー炉システムは、すべてのフェライト生産者にとって標準的な炉となっています。
フェライト業界では、これらの炉は主に低消費電力および高μ値のフェライトに使用され、特に通信業界で使用されます。ベル炉なしでは高品質の中子を製造することは不可能です。
ベル炉は焼結時の作業員が少なく、搬入・搬出は日中、焼結は夜間に完了できるため、電力のピークカットが可能となり、電力不足の昨今において非常に実用的です。ベルジャー炉は高品質の製品を生産し、高品質の製品により追加投資はすべてすぐに回収されます。温度と雰囲気の制御、炉の設計、炉内の気流制御がすべて完全に統合されており、製品の均一な加熱と冷却が保証されます。冷却中のキルン雰囲気の制御はキルン温度に直接関係しており、酸素含有量を 0.005% 以下に保証することができます。そして、これらは競合他社にはできないことです。
完全な英数字プログラミング入力システムのおかげで、長時間にわたる焼結プロセスを簡単に再現できるため、製品の品質が保証されます。製品を販売する場合、それは製品の品質を反映するものでもあります。
熱処理技術
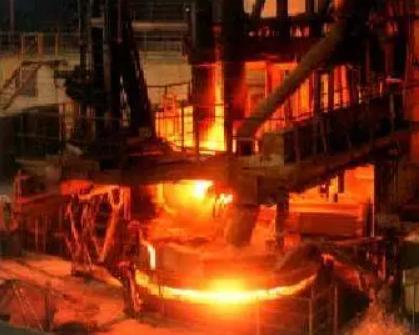
錫-リン青銅など、深刻なデンドライト偏析や鋳造応力を伴う一部の合金インゴット (ストリップ) は、特殊な均質化焼鈍を受ける必要があり、通常はベル ジャー炉で行われます。均質化焼鈍温度は一般に600~750℃の間です。
現在、銅合金条材の中間焼鈍(再結晶焼鈍)および仕上げ焼鈍(製品の状態や性能を制御するための焼鈍)の多くはガス保護による光輝焼鈍を行っています。炉の種類には、ベルジャー炉、エアクッション炉、縦型トラクション炉などが含まれます。酸化焼鈍は段階的に廃止されています。
熱処理技術の発展傾向は、析出強化合金材料の熱間圧延オンライン溶体化処理とその後の変形熱処理技術、保護雰囲気中での連続光輝焼鈍および引張焼鈍に反映されています。
焼入れ - 時効熱処理は、主に銅合金の熱処理可能な強化に使用されます。熱処理により、製品の微細構造が変化し、必要な特殊な特性が得られます。高強度、高導電性合金の開発に伴い、焼入れ時効熱処理プロセスの適用はさらに拡大すると考えられます。時効処理装置はアニール装置とほぼ同様です。
押出技術
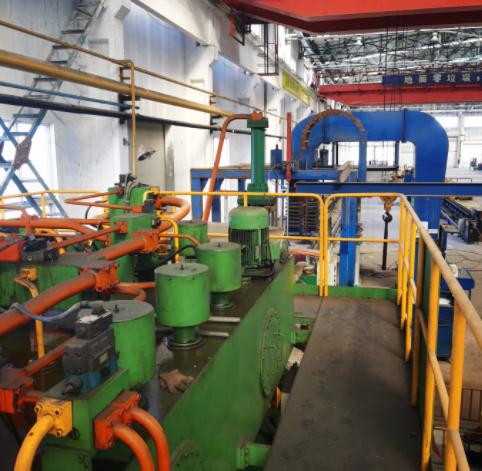
押出成形は、成熟した先進的な銅および銅合金のパイプ、ロッド、異形材の製造およびビレットの供給方法です。金型の変更や有孔押出法を用いることで、様々な合金種や異なる断面形状を直接押出することができます。押出成形により、インゴットの鋳造組織が加工組織に変化し、押出された管ビレットおよび棒ビレットは寸法精度が高く、組織が微細で均一です。押出法は国内外の銅管・銅棒メーカーで一般的に採用されている製造方法です。
銅合金の鍛造は、我が国の機械メーカーが主に行っており、主に大型歯車、ウォームギア、ウォーム、自動車シンクロナイザーギアリングなどの自由鍛造と型鍛造が含まれます。
押出法は順押出、逆押出、特殊押出の3種類に分けられます。その中でも順押出は用途が多く、逆押出は中小型の棒材や線材の製造に、特殊押出は特殊な生産に使用されます。
押出成形の際、合金の特性、押出製品の技術的要件、押出機の能力と構造に応じて、インゴットの種類、サイズ、押出係数を合理的に選択して、変形の程度が適切になるようにする必要があります。 85%以上。押出温度と押出速度は押出プロセスの基本パラメータであり、適切な押出温度範囲は金属の塑性図と状態図に従って決定する必要があります。銅および銅合金の場合、押出温度は一般に 570 ~ 950 °C の間であり、銅からの押出温度は 1000 ~ 1050 °C にも達します。押出シリンダーの加熱温度が400~450℃であるのに比べ、両者の温度差は比較的大きい。押出速度が遅すぎると、インゴット表面温度の低下が早くなり、メタルフローの不均一性が増大し、押出荷重の増加を招き、さらにはボーリング現象を引き起こす可能性があります。 。したがって、銅および銅合金は一般に比較的高速の押出を使用し、押出速度は50 mm/s以上に達することがあります。
銅および銅合金を押出成形する場合、インゴットの表面欠陥を除去するために剥離押出が使用されることが多く、剥離厚さは1〜2μmです。押出ビレットの出口には一般的に水封が施されており、押出後の製品を水槽内で冷却することができ、製品の表面が酸化せず、その後の冷間加工を酸洗いなしで行うことができます。生産効率とその後の一連の総合収率を効果的に向上させるために、同期引取装置を備えた大トン数の押出機を使用して、単一重量が 500 kg を超えるチューブまたはワイヤーコイルを押し出す傾向があります。現在、銅および銅合金管の製造には、主に独立穿孔システム(ダブルアクション)とダイレクトオイルポンプトランスミッションを備えた横型油圧前進押出機が採用されており、棒材の生産には主に非独立穿孔システム(シングルアクション)とオイルポンプダイレクトトランスミッション。横型油圧式前進または後進押出機。一般的に使用される押出機の仕様は8~50MNですが、現在ではインゴットの単体重量を増加させ、生産効率と歩留まりを向上させるために40MNを超える大トン数の押出機で生産される傾向にあります。
最新の水平油圧押出機は、プレストレスト一体型フレーム、押出バレル「X」ガイドとサポート、内蔵穿孔システム、穿孔ニードル内部冷却、スライドまたはロータリー ダイ セットと高速ダイ交換装置、高出力可変オイル ポンプ ダイレクトを構造的に備えています。ドライブ、統合ロジックバルブ、PLC制御などの先進技術を採用し、高精度、コンパクトな構造、安定した動作、安全なインターロック、簡単にプログラム制御を実現できます。連続押出(コンフォーム)技術は過去 10 年間である程度の進歩があり、特に電気機関車用ワイヤーなどの特殊形状の棒材の製造においては非常に有望です。ここ数十年で、新しい押出技術が急速に発展し、押出技術の発展傾向は次のように具体化されています。 (1) 押出装置。押出プレスの押出力はより大きな方向に発展し、30MN以上の押出プレスが主体となり、押出プレス生産ラインの自動化は引き続き改善されます。現代の押出機はコンピュータープログラム制御とプログラマブルロジック制御を全面的に採用しており、生産効率が大幅に向上し、作業員も大幅に削減され、押出生産ラインの自動無人化も実現可能となっています。
押出機の本体構造も継続的に改良され、完成されました。近年、一部の横型押出機では、全体の構造の安定性を確保するためにプレストレストフレームを採用しています。最新の押出機は、順方向および逆方向の押出方法を実現します。押出機には 2 本の押出シャフト (メイン押出シャフトとダイシャフト) が装備されています。押出中、押出シリンダーは主軸とともに移動します。このとき、製品の流出方向は主軸の移動方向と一致し、ダイス軸の相対移動方向とは逆方向になります。押出機のダイベースもマルチステーション構成を採用しており、ダイ交換が容易なだけでなく、生産効率も向上します。最新の押出機はレーザー偏差調整制御装置を使用しており、押出中心線の状態に関する効果的なデータが得られるため、タイムリーかつ迅速な調整に便利です。作動媒体として油を使用する高圧ポンプ直動式油圧プレスは、油圧プレスに完全に取って代わりました。押出ツールも押出技術の発展に合わせて常に更新されています。内部水冷ピアシングニードルの採用が大幅に推進され、異形断面ピアシングローリングニードルにより潤滑効果が大幅に向上しました。長寿命で表面品質の高いセラミック金型や合金鋼金型が広く使用されています。
押出ツールも押出技術の発展に合わせて常に更新されています。内部水冷ピアシングニードルの採用が大幅に推進され、異形断面ピアシングローリングニードルにより潤滑効果が大幅に向上しました。長寿命で表面品質の高いセラミック金型や合金鋼金型の使用が一般的です。(2) 押出成形の製造工程。押出成形品の種類や仕様は日々拡大しています。小断面、超高精度のチューブ、ロッド、異形材、および超大型異形材の押出成形により、製品の外観品質が保証され、製品の内部欠陥が減少し、幾何学的損失が減少し、押出成形品の均一な性能などの押出方法がさらに促進されます。製品。最新の逆押出技術も広く使用されています。酸化しやすい金属にはウォーターシール押出法が採用されており、酸洗い汚染を軽減し、金属損失を減らし、製品の表面品質を向上させることができます。急冷が必要な押出製品の場合は、適切な温度を制御するだけで済みます。ウォーターシール押出法は目的を達成し、生産サイクルを効果的に短縮し、エネルギーを節約します。
押出機の能力と押出技術の継続的な改善により、等温押出、冷却ダイ押出、高速押出およびその他の前方押出技術、逆押出、静水圧押出などの最新の押出技術が徐々に適用されてきました。連続押出技術の実用化プレスとコンフォームの技術開発、低温超電導材料の粉末押出・積層複合押出技術の応用、半固体金属押出やマルチブランク押出などの新工法の開発、小型精密部品の冷間押出成形技術の開発、などが急速に開発され、広く開発および適用されています。
分光計
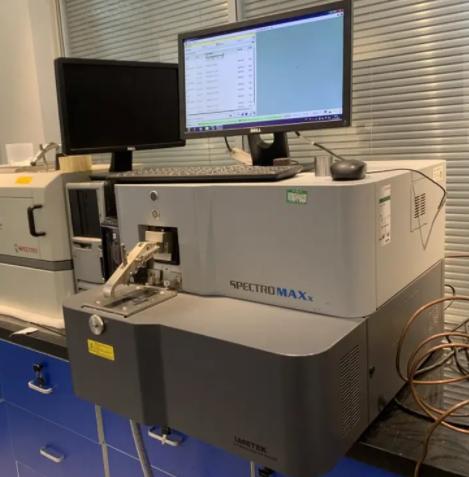
分光器は、複雑な組成の光をスペクトル線に分解する科学機器です。太陽光に含まれる7色の光は、肉眼で識別できる部分(可視光)ですが、太陽光を分光器で分解し、波長ごとに整理すると、可視光はスペクトルのごく一部の範囲を占めるだけで、残りはスペクトルの一部になります。赤外線、マイクロ波、紫外線、X線など、肉眼では区別できないスペクトル。光学情報は分光計によって捕捉され、写真フィルムで現像されるか、コンピュータ化された自動ディスプレイによって表示および分析されます。記事にどのような要素が含まれているかを検出するための数値機器。この技術は、大気汚染、水質汚染、食品衛生、金属工業などの検出に広く使用されています。
分光計は分光計としても知られており、直接読み取り分光計として広く知られています。光電子増倍管などの光検出器を使用して、さまざまな波長のスペクトル線の強度を測定するデバイス。これは、入口スリット、分散システム、結像システム、および 1 つまたは複数の出口スリットで構成されます。放射線源の電磁放射線は、分散素子によって必要な波長または波長領域に分離され、選択された波長で強度が測定されます(または特定の帯域を走査します)。モノクロメーターとポリクロメーターの 2 種類があります。
検査機器-導電率計
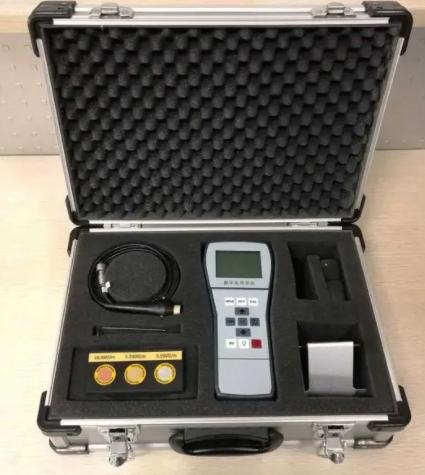
デジタル ハンドヘルド金属導電率テスター (導電率計) FD-101 は、渦電流検出の原理を応用しており、電気業界の導電率要件に従って特別に設計されています。機能と精度の点で金属業界の試験基準を満たしています。
1. 渦電流導電率計 FD-101 には次の 3 つの特徴があります。
1) 航空材料研究所の検証に合格した唯一の中国の導電率計。
2) 航空機産業企業のニーズを満たすことができる唯一の中国の導電率計。
3) 多くの国に輸出されている唯一の中国の導電率計です。
2.製品機能の紹介:
1) 広い測定範囲: 6.9%IACS-110%IACS(4.0MS/m-64MS/m)、すべての非鉄金属の導電率試験に適合します。
2) インテリジェントな校正: 高速かつ正確で、手動による校正エラーを完全に回避します。
3) この機器は優れた温度補正を備えています。測定値は 20 °C での値に自動的に補正され、補正は人的エラーの影響を受けません。
4) 優れた安定性: 品質管理のための個人的なガードです。
5) 人間化されたインテリジェント ソフトウェア: 快適な検出インターフェイスと強力なデータ処理および収集機能を提供します。
6) 便利な操作性: 生産現場や実験室のどこでも使用でき、大多数のユーザーの支持を得ています。
7) プローブの自己交換: 各ホストには複数のプローブを装備することができ、ユーザーはいつでもプローブを交換できます。
8) 数値分解能: 0.1%IACS (MS/m)
9) 測定インターフェースには、%IACS と MS/m の 2 つの単位で測定値が同時に表示されます。
10) 測定データを保持する機能を備えています。
硬さ試験機
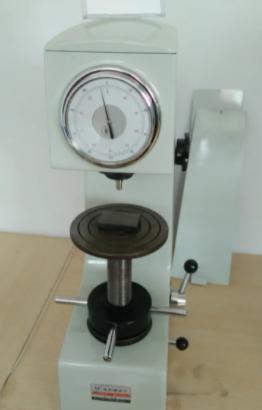
この機器は、力学、光学、光源において独自で精密な設計を採用しており、これにより圧痕イメージングがより鮮明になり、測定がより正確になります。20 倍と 40 倍の対物レンズの両方が測定に参加できるため、測定範囲が広くなり、アプリケーションがより広範囲になります。この機器にはデジタル測定顕微鏡が装備されており、試験方法、試験力、押し込み長さ、硬度値、試験力保持時間、測定時間などを液晶画面に表示でき、接続可能なネジ付きインターフェースを備えています。デジタルカメラやCCDカメラまで。国産ヘッド製品の中でも一定の代表性を持っています。
試験装置-比抵抗検出器
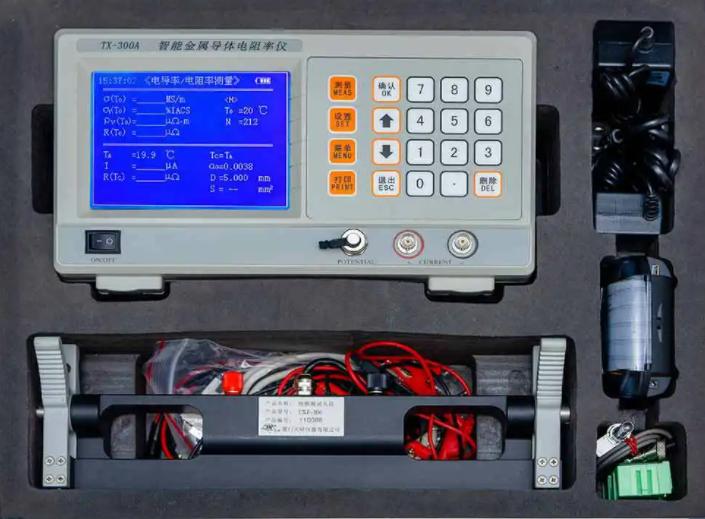
金属線抵抗率測定器は、ワイヤ、棒抵抗率、電気伝導率などのパラメータを測定する高性能試験器です。そのパフォーマンスは、GB/T3048.2 および GB/T3048.4 の関連技術要件に完全に準拠しています。冶金、電力、電線およびケーブル、電化製品、大学、科学研究ユニットおよびその他の産業で広く使用されています。
楽器の主な特徴:
(1) 高度な電子技術、シングルチップ技術、自動検出技術を統合し、強力な自動化機能と簡単な操作を備えています。
(2) キーを 1 回押すだけで、計算なしですべての測定値を取得できるため、連続的、高速かつ正確な検出に適しています。
(3) バッテリー駆動の設計、小型、持ち運びが簡単、現場や現場での使用に適しています。
(4) 大画面、大きなフォント、抵抗率、導電率、抵抗およびその他の測定値と温度、テスト電流、温度補償係数およびその他の補助パラメータを同時に表示でき、非常に直感的です。
(5) 1 台のマシンに 3 つの測定インターフェース (導体抵抗率および導電率測定インターフェース、ケーブル総合パラメータ測定インターフェース、およびケーブル DC 抵抗測定インターフェース (TX-300B タイプ)) を備えた多目的機能があります。
(6) 各測定には、定電流の自動選択、自動電流転流、自動ゼロ点補正、自動温度補償補正の機能があり、各測定値の精度を保証します。
(7) ユニークなポータブル 4 端子テスト フィクスチャは、さまざまな材料やさまざまな仕様のワイヤまたはバーの迅速な測定に適しています。
(8) データメモリを内蔵しており、1000 セットの測定データと測定パラメータを記録および保存でき、上位コンピュータに接続して完全なレポートを生成できます。